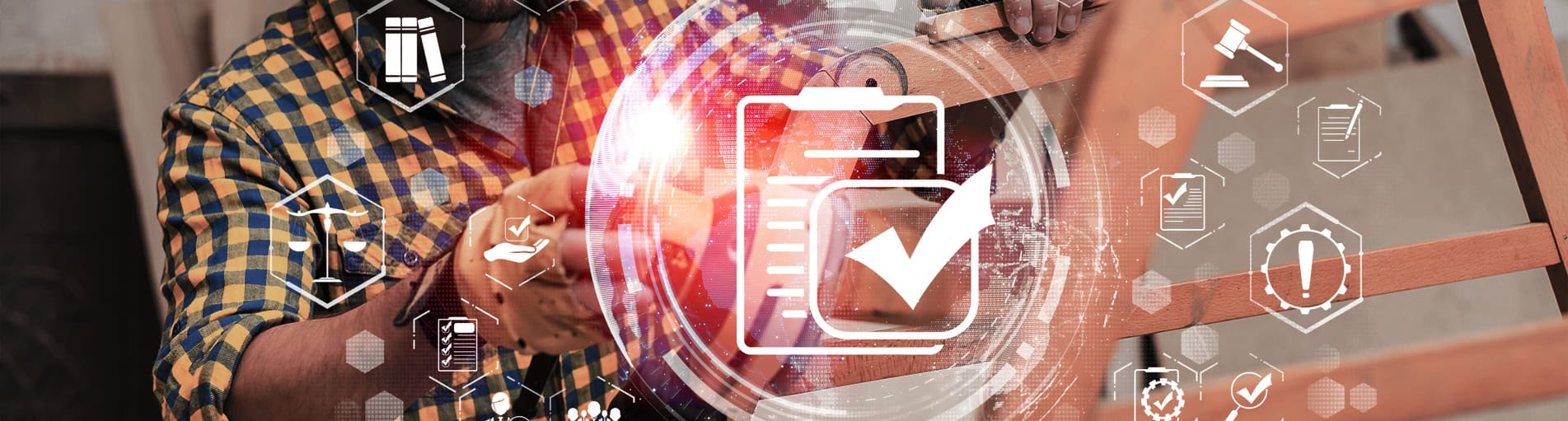
PRODUCT QUALITY COMPLIANCE
What is Product Quality Compliance?
At SBN, we follow a 5-step compliance process after a customer issues a formal order:

COMPLIANCE AND TESTING
• Product compliance ensures products are tested to meet industry standards
• Material compliance makes sure that the timber and chemicals used in the products comply with regulatory requirements
• Supplier compliance – we conduct a social compliance audit to make certain that the supplier meets ethical trade practices and also conduct a technical audit to examine the quality competencies of the supplier.
SAMPLE PREPARATION AND SUBMISSION
Our quality assurance engineer prepares a sample to make sure that the customer’s requirements are met and sends it over to the customer for approval.
TECHNICAL DOCUMENTATION
Our quality assurance engineer will prepare technical documents with helpful technical descriptions and packing instructions, as well as documents with labeling instructions and assembly instructions according to the customer’s requirements.
PRE-PRODUCTION CONFIRMATION (PPC)
Our quality assurance engineer checks the actual product against technical documents to make sure that the product conforms to the customer’s requirements. Any issues detected will be immediately corrected before starting mass production to prevent shipping a non-compliant product to the customer.
FINAL RANDOM INSPECTION (FRI)
All products undergo a final random sampling inspection before shipment through Sourcebynet’s digital inspection system, which is implemented by our highly trained Quality Control Inspectors.
There’s Always A Price to Pay
The path of least resistance (i.e. no Product Quality Compliance) is tempting. After all, who wouldn’t want to cut costs, increase margins, and reduce logistical workload? But for businesses reliant on high customer satisfaction and repeat purchases, the longer term alternative – Product Quality Compliance – is a stronger proposition. Its benefits include the reduction of regulatory risk and increase in product lifecycle and efficiency, eventually snowballing to superior cost savings. If your brand is competing on quality, then a sound quality compliance system is not just a nice-to-have, but an essential differentiator.
Quality Backed by Experience
Where others tick audit checklists, we bring to the table a comprehensive compliance framework. Our product quality compliance model includes supplier selection (audit), product technical design, and sample confirmation (quality assurance) and final inspection (quality control).
This is made possible by our commitment to quality across the supply chain. 75% of Sourcebynet’s employees work in quality functions, bringing together a combined 1000 years of furniture inspection experience. We have made more than 50,000 product inspections in over 20 years of operating in China, South East Asia, Eastern Europe, and South America. We are proud that we have a claim record of less than 2% in some of the most cost-conscious, quality sensitive segments of the global furniture retail market.
Through our structured process, dedicated staff and use of advanced technology to give us unsurpassed access to information and analysis of quality issues, we continue to deliver exceptional quality control – just ask our clients and their satisfied customers.